Properties Nitrotec®
A surface hardening process for steel and cast iron, carried out in a gas oven, makes the surface resistant to wear and corrosion.
See also the brochures and certificates
properties Nitrotec®
The nitrotec coating of the application has a positive influence on the properties of the product as described here.
- Wear resistance
- Surface hardness
- Mechanical properties
- Fatigue strength
- Tread (Tribological) properties
- Corrosion resistance
- Surface condition
- Aesthetic properties
- Good dimensional and shape stability
- Alternative to hard chrome plating
- Weight reduction
- Cost saving
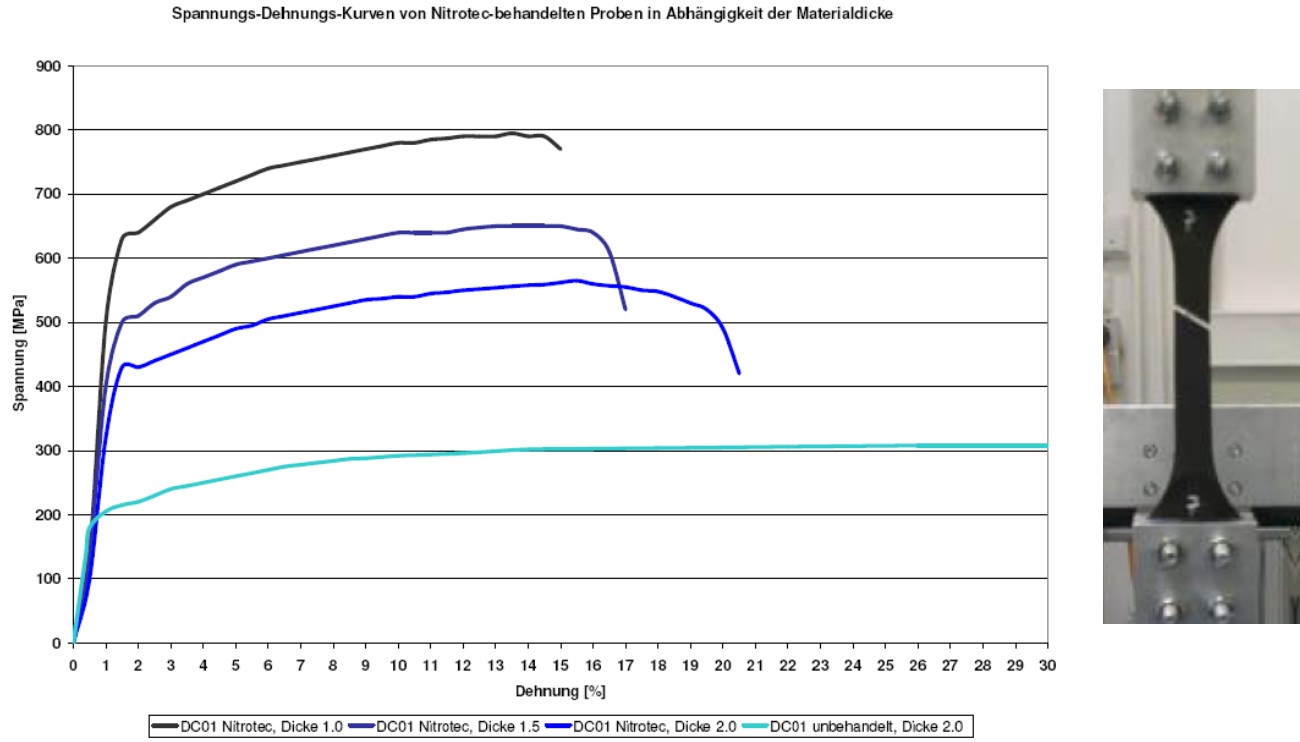
wear resistance
The high surface hardness in combination with the composition of the bonding layer and the presence of the micro pores, which can absorb and release lubricants, result in excellent wear resistance.
pressure resistance (hardness)
The hardness of both the connection layer and the hardness of the edge zone are indicative of the resistance to lasting compression caused by a point load.
strength increase
Rapid quenching during the Nitrotec® process significantly increases the strength of thin cross-sections, such as in sheet steel. This results in both an increase in yield strength and in fatigue resistance.
bearing (tribological) properties
Due to the specific composition of the bonding layer, Nitrotec® layers can, in specific cases, interact with each other and with other surface substrates without additional lubrication.
corrosion resistance
Nitrotec® in combination with an organic sealant, stored in the micro pores of the connecting layer, has a corrosion resistance better than electrolytically coated products and comparable to that of average stainless steel grades. A combination of different surface finishes with a wide range of organic sealant results in a corrosion resistance of at least 240 hours in a salt spray test.
surface condition
The environmentally friendly and clean Nitrotec® treatments guarantee an optimal surface condition.
aesthetic finish (look)
The Nitrotec® process gives an attractive, aesthetic anthracite to black appearance to the application.
dimensional and form stability
With conventional hardening processes, uncontrollable size and shape changes usually occur. These are caused by quenching at high treatment temperatures. During the Nitrotec® process, these structural changes do not occur, thus guaranteeing accurate dimensional and shape tolerances, especially for thin-walled products.
layer composition
The layer formed during the Nitrotec® process, the so-called connecting zone, is supported by a nitrogen austenite layer. The connecting layer is closed off with an oxide layer, this oxide magnetite, is approx. 1 µm thick and can, if desired, be increased to 4 µm.
The thickness of the connecting layer is also variable depending on the material and application. Under the nitrogen-austenite layer, the so-called diffusion zone is formed.